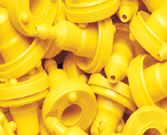
Gas assist injection molding is a relatively low-pressure process (<10,000 psig) utilizing nitrogen gas to apply uniform pressure throughout the molded plastic part. Our experience includes manufacturing reliable, low-maintenance compressors and compressor systems for applications ranging from 1,500 to 10,000 psig (10.3 to 69 MPa).
GAS ASSIST INJECTION MOLDING
FEATURES
- Robust, reliable, low-maintenance design.
- Non-lubricated piston. Does not contaminate the process gas.
- Custom control and piping systems can be quoted for any machine.
- Compressor systems can run unattended and be checked on for periodic maintenance.
- Compressors feature an intensifier with electro-hydraulic power units. This eliminates the need for drive air.
- Patented free piston design allows for maintenance on the high-pressure seals without removing the hydraulic section.
- Water-cooled intensifier allows higher •compression ratios which reduces the number of stages.
- Hydro-Pac gas compressors work over a wide range of inlet pressures. In many cases inlet pressure regulators are not required.
- Standard operating ranges for this line are:
- Discharge pressures: 1,000 to 12,000 psig
- Inlet pressure range: 70 to 6,000 psig
- Capacity ranges: <1 scfm to >300 scfm
- The LX-SERIES compressor can be used for heavy duty low-pressure applications or gas scavenging (reclaim) application to use all of the available gas in the cylinders.